Understanding the 3D Vision System
3D machine and computer vision systems are advanced technologies that enable machines to perceive and understand the three-dimensional aspects of objects in their environment. Unlike traditional 2D computer vision systems, which can only capture flat images, 3D computer and machine vision, system utilize various techniques to capture depth information, allowing for accurate spatial analysis.
By using laser triangulation, structured lighting, or stereo imaging technology, 3d machine learning and machine vision systems can capture detailed depth information of objects, enabling them to identify object shapes, dimensions, and positions accurately.
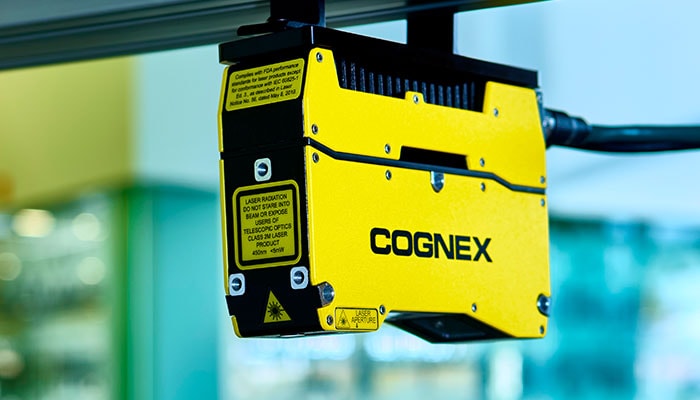
Importance of 3D Machine Vision System in Industrial Applications
Real-time 3D data
In industrial environments, 3D machine vision system play a crucial role in automating processes and enhancing overall efficiency. By providing real-time 3D data, these systems facilitate precise inspection, quality control, and error detection during production. They can detect defects, measure dimensions, verify assembly accuracy, and identify inconsistencies in products, all at high speed and with great accuracy.
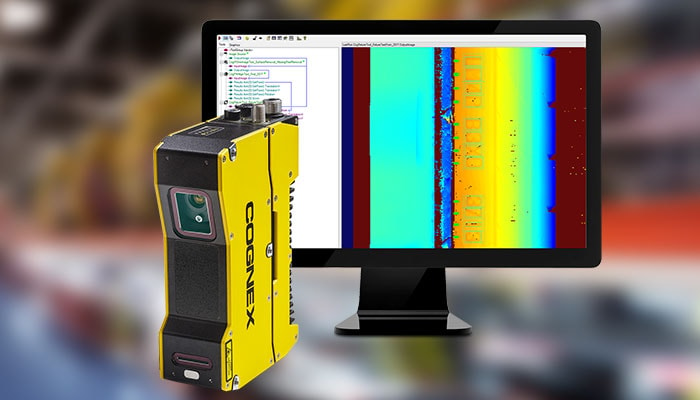
Improving robotic guidance
Furthermore, 3d machine and computer vision systems significantly improve robotic guidance, for example in robot move, enabling robots to navigate complex environments with precision. This machine vision technology allows robots to detect and manipulate objects based on their 3D features position and orientation, for example, making them valuable robot assets in tasks like pick-and-place operations or bin picking.
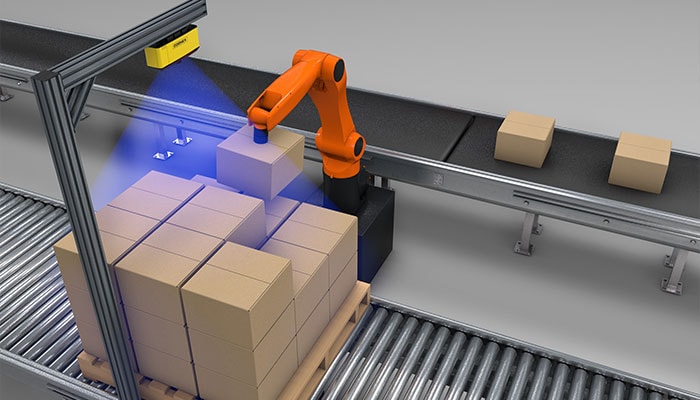
Increased productivity for manufacturers
With the implementation of 3D machine vision inspection system technology, manufacturers witness increased productivity, reduced waste, and cost savings due to minimized errors and improved efficiency. One significant way 3D machine vision systems technologies contribute to increased productivity is by reducing labor costs. Therefore, understanding the fundamentals and applications of 3D machine vision system technology is crucial for industries seeking to harness the power of automation technologies and enhance their manufacturing processes.
Applications of 3D Vision Systems in Manufacturing
Quality Control Enhancement with 3D Vision Systems
Quality control is a critical aspect of any manufacturing process, ensuring that products meet the specified standards and customer expectations. 3d machine vision systems play a vital role in enhancing compliance checking by providing accurate and reliable inspection capabilities. These systems can detect surface defects, measure dimensions, examine geometric tolerances, and detect deviations in manufactured parts.
For instance, the identification and extraction of blobs involve examining an image to detect discrete clusters of connected pixels, such as a black hole within a grey object, serving as landmarks in the image. By comparing captured 3D data with reference models or CAD designs, manufacturers can quickly detect any flaws or variations, enabling timely interventions to sustain the high quality standards of the product.
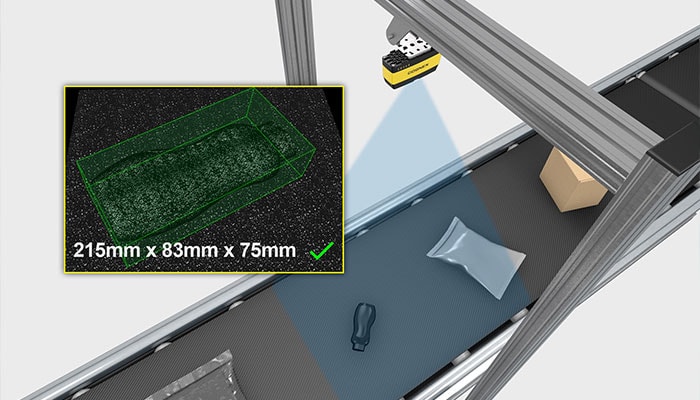
Robotic Guidance and 3D Vision Systems in Manufacturing
The integration of robotics in manufacturing processes brings efficiency and precision, and 3D computer and machine vision systems play a key role in optimizing their performance. With the help of 3D machine and computer vision systems, robots can accurately perceive patterns in their surroundings, create them, track objects, orientation, and make informed decisions based on depth perception.
Additionally, industrial automation machines, collaborative robots, or cobots, equipped with 3d machine vision system can work alongside human operators safely. The accurate depth perception provided by these systems enables cobots to detect and avoid collisions, for example, enhancing workplace safety and security while improving productivity.
Components of a 3D Vision
Role of Cameras in 3D Vision Systems
Cameras form a vital component of 3D machine vision systems, capturing visual data that is subsequently processed to generate 3D models process images and measurements. These cameras are designed to capture images from multiple viewpoints, allowing for the triangulation of three dimensions and depth information. High-resolution camera with precise calibration are essential to ensure accurate and reliable depth perception.
Additionally, cameras in 3D machine vision systems may utilize specialized techniques such as stereo imaging, structured light, lighting, or time-of-flight (TOF) to capture depth information.
Stereo imaging involves the use of two or more cameras placed at different angles to capture overlapping images, which are then analyzed to compute depth by identifying disparities between the images.
Structured light systems project a known pattern of light onto a scene, and the deformation of this pattern as it interacts with objects allows for precise depth measurement.
Proper lighting is crucial in 3D imaging, as it enhances contrast and reduces shadows, improving the accuracy of depth perception.
Time-of-flight (TOF) technology measures the time it takes for a light pulse to travel to an object and back, enabling the calculation of distance based on the speed of light.
They provide the contrast, color and contrast information along with depth data, enabling a comprehensive analysis of the captured image and scene.
Understanding Sensors and Software in 3D Vision Systems
Apart extract information only from camera, 3D machine vision systems incorporate sensors and software to enhance their functionality. Sensors, such as depth sensors or laser scanners, work in conjunction with camera to obtain precise image, location, orientation and depth measurements. These sensors emit infrared or laser light and measure the reflection or time-of-flight of the emitted light to calculate the position and distances accurately.
The software component of a 3D vision camera performs critical tasks such as image processing, point cloud generation, and 3D reconstruction process images. It employs algorithms to analyze the captured image data, to make point cloud, extract information about relevant features, and generate accurate 3D models. The camera software also provides functionalities for object recognition, measurement, and defect detection.
Object recognition
Object recognition is crucial in industrial automation, enhancing efficiency, accuracy, and safety. By enabling machines to identify and process objects accurately, production lines can operate with minimal human intervention, reducing errors and increasing throughput. This technology is essential for quality control, ensuring products meet specifications by detecting defects and inconsistencies. Additionally, object recognition facilitates advanced robotics, allowing for precise handling and assembly tasks. It also supports inventory management through automated tracking and sorting of items.
3D Machine Vision: The Benefits
Improved Accuracy and Precision with 3D Vision
One of the key benefits of implementing a full 3D vision machine system in industrial settings is the significant improvement in measurement accuracy and precision. Traditional 2D vision systems may struggle to focus and capture depth information accurately, leading to potential errors in measurements and inspections. However, with 3D vision systems, the ability to perceive the spatial aspects of item enables highly precise measurements, analysis and inspections.
Moreover, 3D machine vision systems contribute to improved precision in industrial automation and processes. Robots equipped with 3D systems can precisely locate and manipulate objects based on their 3D features, allowing for precise assembly, pick-and-place operations, and intricate tasks.
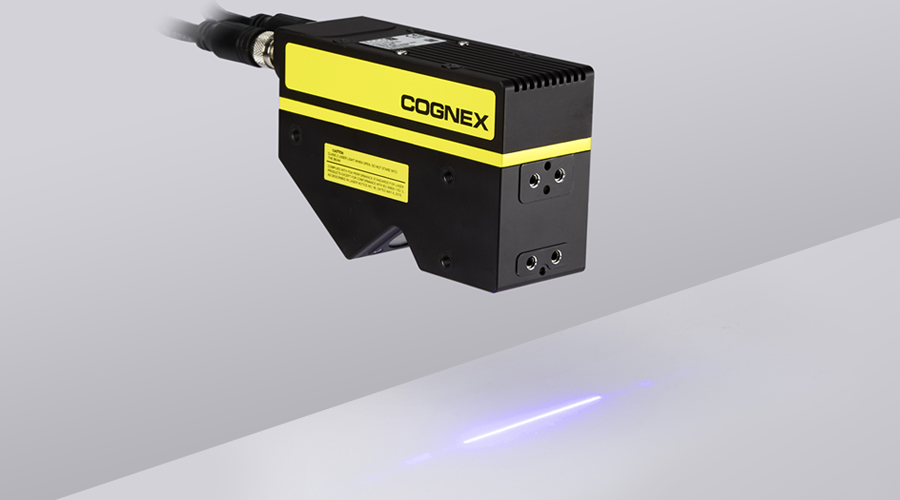
Streamlining Production Processes using 3D Vision
Another significant advantage of implementing a 3D machine vision in production is the ability to streamline production processes. By automating inspection tasks, 3D machine vision systems eliminate the need for manual inspection, reducing human error and increasing overall efficiency and production speeds. Streamlining production processes with 3D vision systems can lead to significant reductions in labor costs.
Furthermore, three dimensions machine vision systems enable real-time on line monitoring to inspect and keep product quality under control during production. Defective or non-conforming products can be swiftly identified and rejected, preventing them from entering the market and minimizing potential recalls.
Overcoming Challenges in Deploying 3D Vision Systems
Integration of the the 3D vision systems with existing systems
One common challenge is the integration of the the 3D vision systems, industrial machine vision, with other existing systems, such as mechanical or quality control software. Ensuring seamless communication and compatibility between different components can be complex.
However, with proper planning and collaboration with system integrators, these challenges can be overcome. Integration solutions may involve customized software development, hardware adjustments, or adapting the company' existing infrastructure to accommodate the 3d machine vision.
Calibrating and aligning the machine vision part and system
Another challenge lies in the process of calibrating and aligning the machine vision part and system accurately to ensure precise and reliable image measurements. Proper calibration requires expertise and may involve complex procedures to ensure optimal performance.
However, calibration techniques, documentation, and support from the machine vision system manufacturers can help manufacturers overcome this challenge.
Training and Expertise for Successful Implementation
Implementing and utilizing 3D machine vision systems effectively require trained personnel who possess the necessary expertise. Training employees on how to operate and maintain the system, interpret the collected data, and troubleshoot potential issues is crucial for successful implementation with the equipment.
Ensuring that operators and technicians are equipped with the knowledge, equipment and skills to utilize the 3d vision system optimally can greatly enhance its benefits.