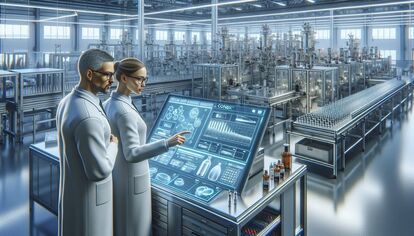
Manufacturing teams in the pharmaceutical, cosmetic, and food & beverage industries face the frustrating reality of lost productivity due to preventable downtime caused by equipment failures. This not only costs time and resources but can also result in significant financial losses and compromise product quality.
Follow these tips to identify and address the key causes of downtime and improve your production efficiency:
1. Equipment Failures
When machines break down unexpectedly, production grinds to a halt, causing major disruptions and delays. To mitigate this issue, it’s essential to be proactive about equipment performance.
- Implement Predictive Maintenance: By using data analytics and monitoring tools, you can predict potential failures before they occur, allowing for timely interventions and minimizing downtime.
- Schedule Regular Inspections: Routine checks can help identify wear and tear early on, ensuring that any necessary repairs are addressed before equipment failures affect production.
- Invest in Quality Equipment: Choosing reliable and durable machinery can reduce the likelihood of failures and the costs associated with repairs and replacements.
2. Inefficient Quality Control
Inadequate quality control processes can result in product defects, leading to waste and unnecessary rework. This inefficiency can significantly slow down the production line.
- Adopt Automated Inspection Systems: Implementing advanced vision systems ensures real-time quality checks, catching defects early and streamlining the production process.
- Standardize Quality Procedures: Clearly defined protocols can help maintain consistency in quality checks, reducing variability and improving operational efficiency.
- Train Teams on Quality Requirements: Ensuring your staff understands quality standards and processes will enhance their ability to identify and address quality issues swiftly.
3. Poor Maintenance
Neglecting machinery upkeep can lead to unexpected breakdowns and costly repairs. Establishing a solid maintenance routine is critical to maintaining productivity.
- Create a Maintenance Schedule: Consistent maintenance plans can help prevent issues before they arise, ensuring machinery runs efficiently.
- Train Staff on Maintenance Practices: Equipping your team with the proper knowledge for maintenance tasks empowers them to address minor issues before they escalate.
- Use Technology for Maintenance Tracking: Integrating software solutions can streamline maintenance management, helping track repairs and schedule inspections more effectively.
4. Inadequate Training
A lack of proper training can lead to errors in operation and maintenance, causing costly downtime. Ensuring your team is well-trained can result in smoother operations.
- Develop Comprehensive Training Programs: Customized training ensures that employees understand the intricacies of the machinery they operate, significantly reducing the chance of operator-related downtime.
- Provide Ongoing Education Opportunities: Regular workshops and courses help keep staff updated on best practices and new technologies.
- Encourage Knowledge Sharing: Creating a culture of sharing experiences and expertise among team members can enhance overall operation efficiency.
5. Supply Chain Disruptions
Unforeseen supply chain issues can delay production schedules and create significant bottlenecks. Understanding the factors that lead to these disruptions can bolster your responsiveness.
- Diversify Suppliers: Developing relationships with multiple suppliers can reduce the risk of stark disruptions when one source encounters issues.
- Improve Demand Forecasting: Utilizing technology to predict demand can help you better manage inventory and secure materials before shortages occur.
- Collaborate with Logistics Partners: Strengthening partnerships with logistics providers can enhance communication, ensuring that you are informed and can respond quickly to any supply chain concerns.