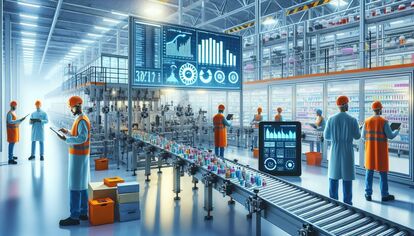
Manufacturers in the pharmaceutical, cosmetic, and food & beverage sectors that neglect the importance of automation often face increased quality issues, leading to costly recalls and damaged reputations. Embracing automation can revolutionize your production processes, ensuring higher quality and consistency.
Follow these tips to ensure you implement automation effectively and enhance your production capabilities:
1. Quality Control
Companies that fail to implement robust quality control measures often experience significant product defects, resulting in customer dissatisfaction and lost sales. Consider leveraging automation to enhance your quality inspection processes.
- Implement Automated Inspections: Utilizing Cognex vision systems allows for real-time monitoring of product quality, catching defects before they reach the consumer. This proactive approach not only boosts confidence in your product but minimizes potential recalls.
- Integrate AI-Powered Analytics: Incorporating artificial intelligence into your quality control process enables smart decision-making based on data patterns. This helps in identifying root causes of defects and driving continuous improvement.
- Train Your Team on Best Practices: Ensure your engineering team understands how to maximize the benefits of automation tech. Regular training keeps your team updated on techniques that improve inspection accuracy and efficiency.
2. Operational Efficiency
Manufacturers that operate with outdated or manual processes often face delays, miscommunication, and bottlenecks, negatively impacting overall productivity. Automation can streamline operations and significantly enhance throughput.
- Adopt Integrated Automation Systems: Use Cognex's automated solutions to synchronize various stages of production, ensuring a seamless flow of materials and information. This reduces lead times and improves overall efficiency.
- Utilize Real-Time Monitoring: Implement real-time monitoring systems to identify inefficiencies as they occur. This allows for immediate corrective actions, minimizing downtime and maximizing output.
- Conduct Efficiency Assessments: Regularly evaluate your production processes to identify areas where automation can be beneficial. Continuous assessment ensures that your operations remain top-notch and eliminate unnecessary waste.
3. Production Costs
Failure to address production inefficiencies often results in skyrocketing costs that eat into profit margins. Investing in automation can significantly lower your operational expenditures in the long run.
- Reduce Labor Costs: With automated inspections and process controls, you can minimize the need for ongoing manual labor, allowing you to allocate resources more effectively. This not only cuts costs but also reduces human error.
- Minimize Waste: Automation helps fine-tune processes, which leads to lower material waste during production. By closely monitoring quality and efficiency, your facility can maximize resource utilization.
- Optimize Inventory Management: Implement systems that synchronize production rates with inventory levels. This automated approach ensures that you're not overproducing, thus keeping costs down.
4. Compliance and Traceability
In an industry where compliance is crucial, manual record-keeping can lead to errors and omissions that can result in hefty fines and damaged credibility. Automation provides the necessary tools to enhance compliance effortlessly.
- Incorporate Automated Reporting: Utilize software that automatically generates compliance reports based on real-time data. This ensures you remain within regulatory guidelines while saving valuable time.
- Implement Traceable Processes: Use integrated systems that maintain detailed logs of every production stage. This traceability provides transparency and assurance that your products meet stringent industry standards.
- Stay Updated on Regulatory Changes: Ensure your automation tools are adaptable to changing compliance regulations. Regularly update your systems to maintain compliance without the need for intensive manual input.
5. Scalability
Companies that struggle to scale often find their manual processes inhibit growth by limiting productivity and response to market demands. Embracing automation enables you to scale operations quickly and efficiently.
- Invest in Modular Automation Solutions: Choose flexible automation technologies that can easily adapt to increased production needs without significant overhauls. This agility keeps your business competitive in a fast-paced market.
- Forecast Production Needs Accurately: Use data analytics from your automated systems to predict sales trends and adjust production schedules accordingly. Proactive planning ensures you're always prepared to meet customer demand.
- Enhance Collaboration Across Departments: Automation can bridge gaps between departments, facilitating communication and resource sharing. As your company grows, having a unified operational approach is crucial for scalability.