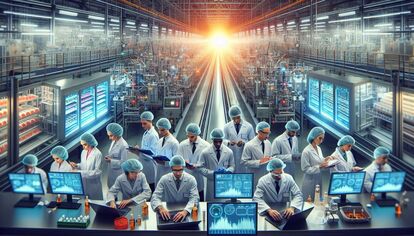
Manufacturers in the pharmaceutical, cosmetic, and food & beverage industries face significant risks as high error rates can lead to costly product recalls and loss of customer trust.
By recognizing these signs of downtime, you can implement solutions to enhance efficiency and maintain quality standards:
1. High Error Rates
High error rates not only signal production inefficiencies but can also result in considerable waste and increased operational costs. To mitigate this issue, consider the following recommendations.
- Implement Automated Inspection: Utilizing Cognex vision systems can drastically reduce human errors by ensuring every product meets quality standards before reaching the market.
- Analyze Error Patterns: Regularly reviewing error reports can help identify common issues and allow for targeted adjustments in production processes to prevent recurrence.
- Train Your Team: Providing ongoing training for your engineers can empower them to effectively operate new technologies and maintain high quality during production.
2. Low Output
Low output levels can reflect underlying inefficiencies and may indicate failing equipment, leading to missed production targets and revenue loss. Leverage the following recommendations to address this concern.
- Conduct Equipment Assessments: Regular checks on your machinery can help identify problems before they escalate and affect production levels.
- Utilize Predictive Maintenance: By implementing maintenance solutions with your vision systems, you can predict failures and schedule repairs without significant process interruptions.
- Optimize Production Scheduling: Analyzing workflow efficiency can help adjust scheduling practices to enhance output without overburdening your team.
3. Frequent Breakdowns
Constant equipment breakdowns can severely disrupt production schedules and impact overall productivity. To combat this, consider the following strategies.
- Invest in Quality Equipment: Ensure you are using reliable and compatible automation technologies such as Cognex vision systems to minimize the likelihood of breakdowns.
- Establish a Maintenance Plan: Scheduling regular maintenance can help keep machinery in optimal condition and reduce unexpected downtime.
- Train Your Staff on Equipment Use: Proper training for your team on the correct operation of machinery can prevent misuse that often leads to breakdowns.
4. Workflow Delays
Workflow delays can stifle your production line and impact delivery timelines, potentially leading to customer dissatisfaction. Here are some actionable recommendations to mitigate delays.
- Map Your Workflow: Creating a visual representation of your production process can help identify bottlenecks and areas for improvement.
- Automate Quality Checks: Integrating automated inspection solutions can streamline inspection processes and reduce delays associated with manual checks.
- Regularly Review Processes: Establishing periodic reviews to assess workflow efficiency can help uncover recurring issues that need resolution.
5. No Real-Time Monitoring
Lack of real-time monitoring can prevent manufacturers from quickly identifying and addressing production issues, leading to increased downtime. Here’s how to enhance monitoring in your facility.
- Implement Real-Time Data Solutions: Utilizing data from Cognex vision systems can provide immediate insights into production performance and alert teams to emerging problems.
- Train Engineers on Data Interpretation: Ensuring your team understands how to analyze production data can help them respond effectively to issues as they arise.
- Integrate Monitoring with Maintenance Alerts: Linking real-time monitoring with maintenance notifications can facilitate proactive responses and minimize potential downtime.