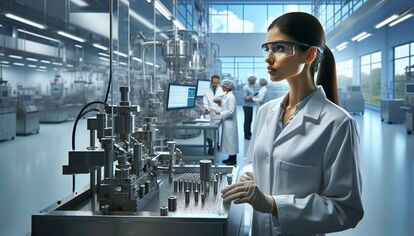
Manufacturers in the pharmaceutical, cosmetic, and food & beverage industries that rely on manual inspection processes face significant risks including costly errors, inefficiencies, and compliance issues.
Follow these tips to mitigate these risks and enhance your inspection processes:
1. Human Error
Manual inspections are prone to human errors, leading to product defects and costly recalls. Consider implementing automated solutions to minimize these mistakes.
- Invest in Automation: Utilize automated quality inspection systems to reduce the risks associated with human error, ensuring consistent accuracy in your inspections.
- Provide Training: Offer comprehensive training for your team on the technologies in use, building confidence and competence while reducing the likelihood of mistakes.
- Implement Double-Checks: Establish a protocol for double-checking critical inspection points, helping to catch and correct errors before they escalate.
2. Inconsistent Standards
Manual processes often lead to varying inspection standards, resulting in inconsistent product quality. Transitioning to a standardized system can solve this issue.
- Establish Standard Operating Procedures (SOPs): Develop and enforce SOPs for inspection processes to ensure uniformity in evaluating product quality across shifts and teams.
- Utilize Automated Systems: Implement automated inspection systems that adhere to defined quality standards, ensuring consistent performance regardless of personnel changes.
- Regularly Audit Inspection Processes: Conduct routine audits to review adherence to standards and make necessary adjustments to your quality control processes.
3. Slow Production
Manual inspections can bottleneck production lines, delaying time-to-market for your products. Adopting more efficient processes can enhance overall productivity.
- Streamline Inspection Workflows: Analyze your current inspection workflow and identify areas for improvement, aiming to reduce time spent on manual checks.
- Integrate Vision Systems: Implement Cognex vision systems to speed up the inspection process, ensuring faster production cycles without sacrificing quality.
- Analyze Production Data: Use data analytics to identify production bottlenecks and optimize your inspection processes for improved efficiency.
4. High Labor Costs
Maintaining a workforce dedicated to manual inspections can lead to inflated labor costs that eat into your margins. Finding efficient alternatives can alleviate this financial burden.
- Adopt Automation: By transitioning to automated inspection solutions, you can significantly reduce the need for extensive manual labor, ultimately lowering your labor costs.
- Cross-Train Employees: Cross-train your workforce on multiple roles to maximize productivity and flexibility, reducing the dependency on a large inspection team.
- Evaluate ROI of Inspection Processes: Analyze the return on investment for manual inspections versus automated systems to make informed decisions on resource allocation.
5. Compliance Challenges
Inconsistent compliance with industry regulations can lead to costly penalties and damage your reputation. Automating inspections can help maintain compliance more effectively.
- Implement Automated Reporting: Use automated systems to generate accurate reports that meet regulatory requirements, ensuring compliance and reducing the risk of violations.
- Stay Informed on Regulations: Regularly train your team on current industry regulations to ensure everyone is aware of compliance standards affecting your processes.
- Conduct Regular Compliance Reviews: Schedule periodic reviews of inspection processes to ensure they align with the latest regulations and adapt to any changes in industry standards.
6. Limited Data Analysis
Relying on manual inspections restricts data collection and analysis, hampering your ability to make informed business decisions. Leveraging technology opens up new insights.
- Utilize Data Analytics Tools: Integrate advanced analytics tools with your inspection systems to gather and analyze quality data, providing deeper insights into production performance.
- Implement Continuous Improvement Strategies: Use the data collected from automated inspections to continuously refine your production processes and enhance quality.
- Share Insights Across Teams: Encourage cross-department collaboration by sharing inspection data, fostering a culture of continuous improvement throughout your organization.