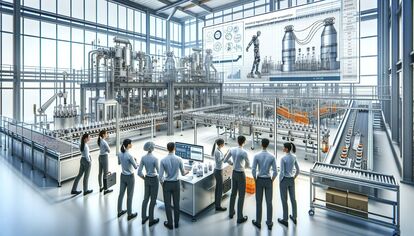
North American companies in the pharmaceutical, cosmetic, and food & beverage industries struggling with manufacturing defects face increased costs, dissatisfied customers, and potentially severe compliance issues.
Follow these tips to address these challenges and enhance your production process:
1. Inadequate Quality Control
Manufacturers often overlook the necessity of a robust quality control process, leading to defects slipping through the cracks. Implementing stricter quality measures can dramatically reduce these errors.
- Establish Clear Standards: Set detailed quality benchmarks to guide your inspection processes and ensure all products meet the required specifications.
- Implement Automated Inspection: Utilize automated systems like Cognex vision solutions to consistently monitor quality levels in real-time, minimizing human error.
- Conduct Regular Audits: Schedule routine quality audits to identify and rectify potential issues before they lead to defective products.
2. Poor Calibration
Calibration issues with manufacturing equipment can lead to inaccurate measurements, resulting in defects. Regular calibration checks can help maintain precision in production.
- Schedule Regular Calibration: Set a routine to calibrate machinery to prevent deviations that could lead to defects.
- Use Quality Calibration Tools: Invest in high-precision instruments that ensure your equipment remains accurate and reliable.
- Train Staff on Calibration Protocols: Equip your team with the knowledge required to perform proper calibration and recognize signs of misalignment.
3. Employee Training Gaps
Inadequately trained employees may lack the skills necessary to maintain quality, leading to avoidable mistakes. Investing in comprehensive training programs can enhance operational efficiency.
- Develop a Training Program: Create continuous training modules that keep employees updated on best practices and technologies like vision systems.
- Utilize On-the-Job Training: Pair new employees with experienced team members to foster hands-on learning and proper techniques.
- Regularly Assess Skills: Periodically evaluate team skills and knowledge to pinpoint areas for improvement and adjust training accordingly.
4. Communication Issues
Poor communication can lead to misunderstandings and errors on the production line, ultimately contributing to defects. Ensuring clear communication channels can mitigate these risks.
- Implement Collaborative Tools: Use technology platforms that facilitate real-time communication among teams to ensure everyone is aligned on production goals.
- Encourage Open Feedback: Foster an environment where employees feel comfortable sharing issues or suggestions that could improve quality.
- Conduct Regular Team Meetings: Schedule consistent meetings to review processes and address any communication gaps that might affect production quality.
5. Raw Material Variability
Variations in raw materials can lead to inconsistent product quality, making it a challenge for manufacturers to maintain standards. Partnering with reliable suppliers can reduce this risk.
- Source Quality Materials: Select suppliers that can consistently provide high-quality raw materials to minimize variability in production.
- Conduct Incoming Quality Inspections: Implement inspection protocols for incoming materials to catch and address quality issues before they enter production.
- Establish Strong Supplier Relationships: Collaborate closely with suppliers to ensure they are aware of your quality expectations and requirements.
6. Predictive Maintenance Gaps
Neglecting predictive maintenance can result in equipment failures and unplanned downtime, leading to defects in manufactured products. Establishing a maintenance plan can enhance overall reliability.
- Create a Maintenance Schedule: Develop a comprehensive maintenance schedule that allows for timely checks and repairs of all production equipment.
- Utilize Predictive Analytics: Employ technologies that analyze equipment performance and predict potential failures before they occur.
- Train Team on Maintenance Best Practices: Ensure your team is equipped with knowledge on proper equipment care and common maintenance tasks to keep production running smoothly.
7. Environmental Factors
Environmental conditions such as temperature and humidity can significantly impact the quality of manufactured products. Monitoring these conditions can mitigate adverse effects.
- Implement Environmental Monitoring Systems: Utilize technology to track and adjust environmental conditions in the production area to ensure optimal quality.
- Assess Facility Conditions Regularly: Conduct routine evaluations of your manufacturing environment to identify and correct factors that could be detrimental to product quality.
- Train Employees on Environmental Control: Educate your workforce on the significance of maintaining proper environmental conditions and their effects on quality.