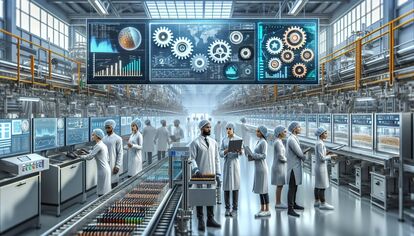
Manufacturers in the pharmaceutical, cosmetic, and food & beverage industries that overlook defect detection risk significant losses from wasted resources, compromised quality, and damaged reputations.
Implementing effective strategies can significantly enhance your ability to identify defects early and maintain high standards of quality.
1. Use Automated Vision Systems for Inspection
Without automated vision systems, human inspection can lead to overlooked defects, resulting in higher costs and customer dissatisfaction. Consider integrating automated solutions to streamline your inspection processes.
- Implement Cognex Vision Systems: These advanced systems provide real-time analysis and precise defect detection, enhancing the reliability of your quality control processes.
- Customize Machine Settings: Tailor the inspection parameters to suit your specific product requirements, ensuring greater accuracy and efficiency in defect identification.
- Schedule Regular System Updates: Regularly update your vision systems to take advantage of the latest advancements in technology for optimal performance and defect detection capabilities.
2. Apply Machine Learning for Defect Detection
Manual defect detection methods can be slow and prone to errors, allowing defects to slip through unnoticed. Leveraging machine learning algorithms can revolutionize your defect detection processes.
- Adopt Predictive Analytics: Utilize machine learning to analyze historical data and predict potential defects, allowing for proactive measures to be taken before issues arise.
- Train Models with Real Data: Use actual production data to train your machine learning models, enhancing their accuracy and effectiveness in detecting defects.
- Continuously Improve Algorithms: Regularly refine and improve your algorithms based on new incoming data, ensuring your defect detection methods remain up-to-date and reliable.
3. Regularly Calibrate Inspection Equipment
Neglecting the calibration of inspection equipment can lead to inconsistencies in defect detection, compromising product quality over time. Establishing a calibration routine is vital for maintaining accuracy.
- Create a Calibration Schedule: Implement a consistent schedule for calibrating all inspection equipment to ensure reliable performance and accurate defect detection.
- Use Standardized Tools: Rely on standardized tools and methods for calibration to maintain the integrity and consistency of your inspection equipment.
- Document Calibration Procedures: Maintain detailed records of calibration activities to track performance and identify trends that may require further attention.
4. Integrate Statistical Process Control
Manufacturers who do not utilize statistical process control may struggle with unpredictability in their production processes, leading to increased defects. Integrating SPC can provide valuable insights into production quality.
- Establish Control Limits: Define statistical control limits to monitor production processes and identify variations that could indicate potential defects.
- Analyze Data Consistently: Regularly analyze production data using SPC techniques to catch anomalies early and minimize defects in the manufacturing pipeline.
- Implement Process Improvement Initiatives: Use insights gained from SPC to initiate targeted process improvements that address identified areas of weakness.
5. Train Quality Control Teams
Inadequately trained quality control teams may not fully understand defect detection techniques, leading to inconsistent quality outcomes. Investing in comprehensive training programs can significantly enhance their effectiveness.
- Develop Training Programs: Create tailored training programs that equip team members with the necessary skills and knowledge for effective defect detection.
- Conduct Hands-on Workshops: Organize practical workshops that allow teams to practice and apply their skills in realistic settings, reinforcing their learning.
- Provide Continuous Learning Opportunities: Encourage ongoing education by offering access to the latest developments in quality control and defect detection strategies.
6. Use Image Processing Techniques
Neglecting the potential of image processing can hinder your ability to detect subtle defects and variations in products. Mastering these techniques can significantly enhance your quality assurance efforts.
- Employ Advanced Algorithms: Use sophisticated image processing algorithms to detect even the smallest defects that the human eye might miss, ensuring high product quality.
- Utilize Open-source Software: Leverage open-source image processing tools to reduce costs while still enhancing your defect detection capabilities.
- Analyze Images in Real Time: Implement real-time image analysis to speed up detection processes and allow for immediate corrective actions when defects are identified.
7. Leverage Data Analytics for Improvement
Manufacturers that fail to harness the power of data analytics may miss out on key insights needed to improve their defect detection processes. Adopting data analytics can transform your approach to quality control.
- Implement Data Monitoring Systems: Set up systems to continuously monitor and analyze production data, providing you with real-time insights into defects and trends.
- Utilize Visualization Tools: Use data visualization tools to make it easier for your teams to identify patterns and anomalies that could signal underlying issues in production.
- Conduct Regular Data Reviews: Schedule regular review sessions to analyze data findings and determine actionable insights for improving defect detection and overall quality.