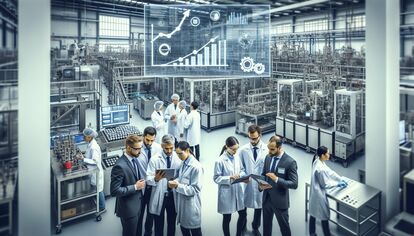
Manufacturing companies in North America that struggle with inefficient processes risk increased waste and reduced profitability. Inefficiencies lead to defects and long production cycles, directly impacting your bottom line.
Follow these tips to pinpoint inefficiencies and optimize your operations:
1. Inefficient Processes
Inefficient processes can create bottlenecks in production, resulting in wasted time and materials. Consider evaluating your workflows and implementing changes to streamline operations.
- Map Your Workflow: Analyze your current processes to identify unnecessary steps that can be removed or simplified.
- Standardize Procedures: Develop clear, standardized procedures to ensure consistency and reduce variability in production.
- Implement Lean Techniques: Use Lean manufacturing principles to minimize waste and maximize productivity by focusing on value-added activities.
2. Lack of Real-Time Data
- Adopt Advanced Analytics: Use data analytics tools to gain insights into your production processes and identify potential problems quickly.
- Integrate IoT Devices: Implement IoT solutions to collect data from various stages of manufacturing for real-time visibility.
- Utilize Dashboards: Create user-friendly dashboards that display key performance indicators (KPIs) for easy monitoring.
3. Inadequate Quality Control
- Establish Stringent QC Protocols: Define clear quality control guidelines for every stage of production to ensure products meet specifications.
- Invest in Automation: Use automated quality inspection systems to reduce human error and enhance consistency in quality checks.
- Conduct Regular Audits: Schedule frequent audits and assessments to continuously monitor and improve your quality control processes.
4. Insufficient Training
A lack of adequate training can lead to mistakes on the production floor, contributing to waste and inefficiencies. Invest in comprehensive training programs for your teams to improve their skills and knowledge.
- Offer Regular Training Sessions: Organize ongoing training for employees to keep them updated on best practices and new technologies.
- Create Training Materials: Develop user-friendly manuals and guides that provide clear instructions on processes and equipment.
- Utilize Mentorship Programs: Establish mentorship opportunities pairing experienced workers with new hires to enhance the learning process.
5. Poor Equipment Maintenance
Neglecting routine maintenance on machinery can result in unexpected breakdowns and costly downtime. Implementing a proactive maintenance plan can help detect issues before they escalate.
- Schedule Regular Maintenance: Create a maintenance schedule that outlines necessary inspections and servicing for all equipment.
- Train Staff on Maintenance Best Practices: Educate your team on the importance of basic maintenance tasks they can perform to prevent equipment failure.
- Invest in Predictive Maintenance Tools: Use IoT sensors to monitor equipment health and predict when maintenance is needed based on real-time data.
6. Supply Chain Disruptions
Supply chain disruptions can lead to material shortages, delaying production and increasing waste. Take proactive steps to mitigate risks associated with your supply chain.
- Diversify Suppliers: Establish relationships with multiple suppliers to reduce reliance on a single source and increase resilience.
- Implement Inventory Management Systems: Use advanced inventory management software to track supplies and forecast needs effectively.
- Foster Communication With Suppliers: Maintain open lines of communication with your suppliers to quickly address and resolve potential disruptions.
7. Inflexible Systems
Inflexible systems can hinder your ability to adapt to changes in demand, leading to overproduction and waste. Embrace flexibility in your manufacturing processes to respond effectively to market needs.
- Adopt Modular Systems: Design manufacturing systems that can be easily adjusted to accommodate varying production requirements.
- Invest in Scalable Solutions: Choose technology solutions that can grow with your business and can be scaled up or down rapidly.
- Implement Agile Practices: Adopt agile manufacturing practices to enhance response times and reduce waste associated with rigid processes.
8. Lack of Automation
A lack of automation in production can lead to higher labor costs and inefficiencies, resulting in increased waste. Consider leveraging automation technology to enhance your operations.
- Invest in Automated Systems: Implement automated machinery to handle repetitive tasks, freeing up human resources for more complex jobs.
- Integrate Robotics: Explore robotic solutions for precision tasks to improve speed and accuracy in production.
- Utilize Vision Systems: Deploy vision systems for quality inspection to enhance consistency and reduce human error in the manufacturing process.