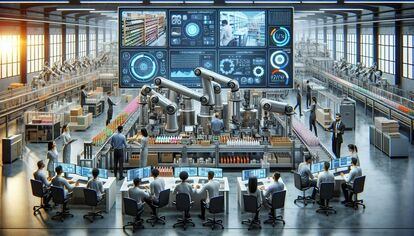
Nobody wants to deal with the financial and reputational consequences of defects in their products, but many manufacturers still struggle with this issue. For North American companies in the pharmaceutical, cosmetic, and food & beverage industries, effectively managing quality can significantly decrease waste and downtime.
Follow these tips to explore technologies that can help solve the problem and enhance your manufacturing line's efficiency:
1. Vision Systems
Manufacturers often face challenges in identifying defects during production, which can lead to costly recalls and diminished customer trust. Utilizing vision systems can dramatically improve defect detection capabilities.
- Implement Cognex Vision Systems: These advanced systems can quickly assess product quality, ensuring that only items meeting high standards pass through. By using automated inspections, you can significantly reduce human error and increase throughput.
- Integrate Into Existing Processes: Vision systems can be seamlessly incorporated into current manufacturing lines, providing real-time feedback and data. This allows for immediate adjustments, minimizing defects right at the source.
- Utilize AI Features: Leverage AI capabilities in vision systems to recognize patterns and variations in products. This technology evolves through data, improving its accuracy and effectiveness over time.
2. Quality Control Software
Inadequate tracking of product quality can result in undetected defects, eroding both profit margins and customer satisfaction. Implementing robust quality control software can streamline this process.
- Develop a Comprehensive QC Program: Quality control software helps in standardizing processes and enhancing traceability across the production line. This ensures that any deviations are detected promptly, preventing larger issues.
- Create Interactive Dashboards: Utilize customizable dashboards to monitor quality metrics in real-time. This allows your team to make data-driven decisions that promptly address potential defects.
- Integrate with Other Systems: Ensure your quality control software can interact with other manufacturing systems for holistic data analysis. This integration optimizes decision-making and enhances quality outcomes.
3. Machine Learning
Manual quality checks can be time-consuming and inefficient, resulting in overlooked defects and increased scrap rates. By adopting machine learning, manufacturers can harness data to optimize quality assurance processes.
- Adopt Predictive Analytics: Using machine learning algorithms allows for predictive modeling regarding defect rates. This means you can anticipate quality issues before they escalate, improving overall product reliability.
- Train Models on Historical Data: Leverage your past production data to train machine learning models that can identify patterns leading to defects. As the model learns, it becomes more adept at spotting potential issues early on.
- Automate Adjustments: Integrate machine learning insights into manufacturing controls to facilitate automated adjustments. This ensures that production is continuously optimized, minimizing defects.
4. Robotics
Labor shortages and human error in repetitive tasks can lead to production inefficiencies and defects. Integrating robotics into manufacturing processes can alleviate these concerns.
- Automate Repetitive Tasks: Robotics can take over repetitive tasks that are prone to human error, such as pick-and-place operations. This not only increases efficiency but also enhances consistent quality.
- Incorporate Advanced Sensors: Equip robots with sensors to monitor product quality during handling. This way, robots can immediately reject defective items, maintaining higher quality standards.
- Utilize Data Feedback Loops: Implement systems where robots can learn from quality data. This ability to adapt leads to continual improvements in the manufacturing process.
5. Sensor Technologies
The absence of real-time monitoring can result in undetected issues that compromise product quality. Innovative sensor technologies can bridge this gap.
- Integrate Smart Sensors: Employ sensor technologies that can monitor environmental conditions and product parameters in real-time. This proactive approach helps identify potential defects or process deviations early.
- Use Data for Continuous Improvement: Consolidate sensor data to track trends and implement adjustments before defects arise. This ensures a higher standard of quality throughout production.
- Implement Wireless Sensor Networks: Design a wireless network for sensors that can communicate critical data instantaneously. This speeds up reaction times to any potential quality issues.
6. Process Control Tools
Inconsistent processes can lead to variations in product quality, causing defects. Process control tools can monitor and regulate these variances effectively.
- Adopt Statistical Process Control (SPC): Use SPC tools to analyze process data and maintain product quality within specified limits. This helps reduce defects and variation significantly.
- Utilize Control Charts: Implement control charts to visualize process performance and identify trends. These charts allow for quick interventions when quality drifts outside acceptable thresholds.
- Incorporate Root Cause Analysis Tools: Use tools for root cause analysis to identify underlying issues affecting quality. Understanding these root issues can help develop corrective actions and improve processes.
7. Manufacturing Execution Systems
Disconnected systems can lead to inefficiencies and errors in product quality. Manufacturing Execution Systems (MES) provide a solution for synchronizing and optimizing operations.
- Implement MES for Real-time Monitoring: Utilize MES to gain visibility into every aspect of production, allowing instant identification of quality issues before they escalate.
- Synchronize Operations: Use MES to ensure that all manufacturing components—from machines to workers—are aligned and working toward quality objectives.
- Analyze Performance Data: Leverage performance data collected by MES to identify bottlenecks and inefficiencies impacting product quality. This facilitates continuous improvement initiatives.
8. Simulation Software
The inability to predict the outcome of changes in manufacturing processes can lead to unanticipated defects. Simulation software can help mitigate these risks.
- Use Simulations for Process Optimization: Implement simulation software to model and test changes in production before implementation. This can significantly reduce the risk of defects arising from process modifications.
- Train Teams with Virtual Scenarios: Utilize simulation tools for training purposes, allowing teams to encounter various operational challenges in a virtual setting. This builds expertise without impacting actual production quality.
- Assess Impact of New Technologies: Employ simulation software to analyze how the integration of new technologies may affect existing processes. This foresight enables informed decision-making for better quality outcomes.