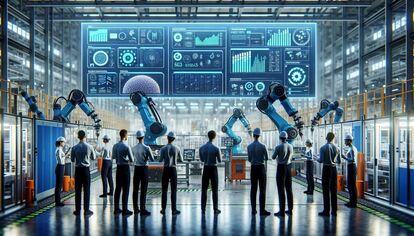
Manufacturing companies in the pharmaceutical, cosmetic, and food & beverage sectors that ignore the latest technologies to reduce defects are risking poor product quality, costly recalls, and damaged reputations.
Embrace these cutting-edge solutions to minimize defects and enhance your production process:
1. Vision Inspection Systems
Companies struggle to catch defects early in the production line, resulting in increased waste and customer dissatisfaction. Implementing robust vision inspection systems can help identify these issues before products leave the facility.
- Assess Your Needs: Evaluate the specific requirements of your production environment to select the right vision inspection system tailored to your processes.
- Integrate with Existing Systems: Ensure that your new vision inspection technology can seamlessly connect with your current manufacturing systems to enhance efficiency.
- Train Your Team: Provide adequate training for your team to effectively use and maintain the vision inspection systems, ensuring maximal utility.
2. Machine Learning Maintenance
Unexpected machinery failures can lead to costly downtimes and production delays, affecting overall productivity. Leveraging machine learning for predictive maintenance can preempt these failures and optimize operations.
- Analyze Historical Data: Review your machinery's past performance data to identify failure patterns and apply predictive analytics.
- Implement Predictive Tools: Utilize machine learning tools to create predictive models that can forecast equipment malfunctions.
- Monitor Real-Time Performance: Continuously monitor equipment in real-time to adapt maintenance schedules and prevent unplanned downtimes.
3. Data Analytics for Quality
Manufacturers often lack the insights needed to implement effective quality control, resulting in undetected defects. Utilizing data analytics empowers companies to enhance quality assurance processes significantly.
- Collect Quality Data: Gather data throughout your production process to pinpoint defect sources and trends.
- Analyze for Insights: Utilize analytical tools to analyze quality data and identify actionable insights to mitigate defects.
- Set KPIs and Goals: Establish key performance indicators (KPIs) based on data analytics to set quality improvement targets.
4. Robotics for Assembly
Labor shortages and inconsistencies in manual assembly can lead to increased defect rates. Implementing robotics in the assembly line can streamline operations and improve product quality.
- Evaluate Robot Types: Determine the best robotics solutions that fit your specific assembly tasks, ensuring compatibility with your products.
- Integrate with Existing Lines: Ensure that the robotics systems can easily integrate into your current manufacturing processes for minimal disruption.
- Train Personnel: Effectively train assembly personnel to work alongside robotics to maximize productivity and engagement.
5. Smart Sensors Monitoring
Without real-time monitoring, manufacturers may struggle to detect anomalies in their production process. Smart sensors can provide crucial data that helps ensure product consistency and quality.
- Identify Key Metrics: Determine which metrics are vital for monitoring your production quality and health.
- Deploy Smart Sensors: Install smart sensors that can gather relevant data continuously, leading to real-time insights.
- Regularly Review Data: Consistently analyze data gathered from smart sensors to immediately address any detected quality issues.
6. Process Control Software
Inconsistent production processes can lead to significant variations in product quality. Adopting advanced process control software can standardize operations and minimize defects.
- Standardize Processes: Use software to develop standardized operating procedures (SOPs) to reduce variability in production.
- Automate Adjustments: Implement software that can automatically adjust production parameters based on real-time feedback, ensuring consistent quality standards.
- Train Users Efficiently: Conduct comprehensive training sessions for your team to understand and utilize the process control software effectively.
7. Internet of Things (IoT)
The lack of connectivity in manufacturing processes can limit visibility and control over production lines. Utilizing IoT devices can enhance data sharing and interconnectivity within your operations.
- Identify Application Areas: Determine which areas in your manufacturing processes will benefit most from IoT connectivity.
- Implement IoT Solutions: Integrate IoT devices to facilitate real-time communication among your machinery and personnel.
- Leverage Data from IoT: Utilize the data collected through IoT devices to optimize production processes and eliminate defects.
8. Augmented Reality Training
Siloed knowledge and inconsistent training can lead to operational inefficiencies and errors. Augmented reality (AR) technology can provide immersive training experiences that enhance learning and retention.
- Develop AR Training Modules: Create customized AR training programs that focus on the specific challenges faced in your production environment.
- Incorporate Interactive Elements: Include interactive elements in your AR training to engage employees actively and improve their understanding.
- Continuously Update Content: Regularly update AR training content based on new technologies and operational changes to keep your team informed.