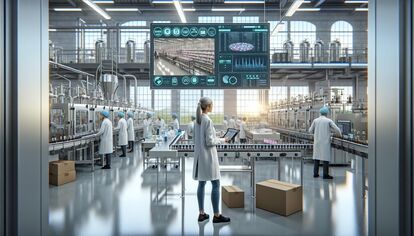
Manufacturers in the pharmaceutical, cosmetic, and food & beverage industries face the risk of unchecked defects, resulting in wasted resources and compromised product integrity.
Follow these tips to enhance your quality control processes and ensure your products meet the highest standards:
1. Implement an Inspection System
Without a structured inspection system, quality issues can slip through the cracks, leading to costly recalls and reputational damage. Consider establishing a thorough system to detect defects before they reach customers.
- Define Inspection Points: Designate specific points along your production line to implement inspections, ensuring problems are caught early and efficiently.
- Standardize Procedures: Create standardized inspection protocols that your team can easily follow, reducing variability and increasing reliability in quality checks.
- Utilize Automation: Integrate automated inspection solutions to enhance speed and accuracy, allowing your team to focus on more complex quality issues.
2. Use Imaging Technologies
Relying solely on human inspection can lead to oversight, as fatigue and distraction are inevitable. Adopting advanced imaging technologies can significantly improve defect detection.
- Integrate Vision Systems: Deploy Cognex vision systems that provide high-resolution imaging to detect even the smallest defects in your products automatically.
- Implement Barcode Scanning: Utilize barcode scanning to verify product specifications and batch tracking, ensuring compliance with industry standards.
- Leverage AI Algorithms: Use AI algorithms in your imaging technologies to predict defects and improve overall product quality through continuous learning.
3. Set Quality Standards
A lack of clearly defined quality standards can result in inconsistent product quality, undermining customer trust and satisfaction. Establishing clear, measurable quality standards helps align your team and processes.
- Develop Specifications: Create comprehensive product specifications that detail acceptable quality levels, helping streamline inspections and enhance accountability.
- Benchmark Industry Standards: Research and adopt industry best practices to ensure your quality standards meet or exceed market expectations.
- Regularly Review Standards: Conduct periodic reviews of your quality standards to adapt to changes in regulations, technology, and customer expectations.
4. Train Your Team
Inadequate training can leave employees unprepared to identify and address quality control issues. Continuous training fosters a knowledgeable workforce capable of maintaining high-quality standards.
- Conduct Workshops: Organize regular workshops to enhance your team's understanding of quality control processes and the importance of consistency in their roles.
- Provide Practical Training: Implement hands-on training sessions that allow team members to practice using inspection equipment and techniques for better retention.
- Encourage Cross-Training: Promote cross-training among teams to enhance understanding of quality control measures across different departments, fostering collaboration and shared responsibility.
5. Analyze Quality Data
Ignoring quality data can result in recurring defects that drain resources and diminish customer satisfaction. Regular analysis of quality data is essential to uncover root causes and make informed improvements.
- Establish KPIs: Define key performance indicators (KPIs) to quantify quality metrics, enabling your team to assess performance against established benchmarks.
- Utilize Statistical Tools: Employ statistical process control tools to analyze trends and identify potential quality issues before they escalate into significant problems.
- Implement Data Dashboards: Create interactive data dashboards that provide real-time insights into quality metrics, enhancing decision-making and responsiveness.
6. Maintain Inspection Equipment
Neglecting inspection equipment can lead to inaccuracies, putting product quality at risk. Regular maintenance ensures reliability and precision in quality control processes.
- Schedule Regular Calibration: Implement a schedule for regular calibration of your inspection equipment to guarantee its accuracy and extend its lifespan.
- Conduct Preventive Maintenance: Establish a preventive maintenance program to address wear and tear before it affects inspection capabilities, minimizing downtime and costs.
- Document Maintenance Activities: Keep detailed records of all maintenance and calibration activities, ensuring compliance with industry regulations and enhancing accountability.
7. Promote a Quality Culture
Employees disinterested in quality control can lead to widespread issues and a lack of accountability. Cultivating a quality-centric culture fosters ownership and pride in product integrity.
- Incorporate Quality Goals: Integrate quality goals into organizational objectives, encouraging employees to prioritize quality in their daily tasks.
- Recognize Quality Champions: Celebrate team members who consistently excel in quality control, reinforcing positive behaviors and motivating others to follow suit.
- Facilitate Open Communication: Encourage open dialogue about quality control practices, allowing employees to share insights and collaborate on improvement initiatives.
8. Work with Automation Experts
Many manufacturers struggle to effectively implement automation solutions due to a lack of expertise, resulting in missed opportunities for improved efficiency and quality. Partnering with automation experts can streamline integration and enhance overall processes.
- Engage Cognex Automation Specialists: Collaborate with Cognex experts to tailor inspection solutions that fit seamlessly into your existing manufacturing process.
- Leverage Best Practices: Gain insights from automation specialists on best practices for integrating quality inspection technologies to maximize their effectiveness.
- Stay Current with Innovations: Maintain a relationship with automation experts to stay informed about the latest technologies and improvements in quality control systems.