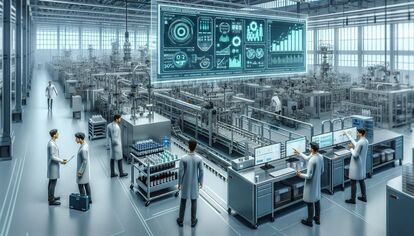
Manufacturers in the pharmaceutical, cosmetic, and food & beverage sectors often struggle with unseen waste that erodes profit margins and hampers productivity.
Implementing effective measurement methods can help you uncover and reduce these inefficiencies, leading to improved yield and quality.
1. Vision Systems for Monitoring
Without real-time monitoring, defects and waste may go undetected, leading to higher costs and lower quality products. Consider integrating advanced monitoring solutions to address this issue.
- Implement Cognex Vision Systems: These systems provide precise visual inspection, identifying defects and inconsistencies as they occur, significantly reducing waste and enhancing product quality.
- Utilize Automated Alerts: Set up alerts for anomalies detected by the vision system to allow for immediate corrective actions, thus minimizing downtime and production losses.
- Integrate with Production Line Systems: By connecting vision systems to existing manufacturing equipment, you streamline operations and enhance overall process visibility.
2. Regular Process Audits
Inefficient processes can lead to increased waste and production costs if not regularly assessed. Conducting audits helps identify areas of improvement to optimize operations.
- Schedule Monthly Audits: Consistent reviews of your processes can uncover hidden inefficiencies and waste, providing crucial insights for improvements.
- Engage Cross-Functional Teams: Involving diverse teams in audits ensures comprehensive evaluations and fosters innovative solutions to eliminate waste.
- Use Audit Tools: Leverage specialized tools and software to streamline the audit process, making it easier to analyze data and track changes over time.
3. Six Sigma Analysis
Manufacturers often face variability that leads to defects and inefficiencies, which can hinder quality control. Applying Six Sigma methodologies can effectively reduce these issues.
- Train Your Team: Equip your engineering team with Six Sigma training to identify root causes of waste and implement effective solutions to enhance process control.
- Utilize DMAIC Methodology: Apply the Define, Measure, Analyze, Improve, and Control framework to systematically eliminate waste and improve overall processes.
- Set Waste Reduction Goals: Establish specific targets for reducing waste and track progress using Six Sigma tools to maintain focus and accountability.
4. Key Performance Indicators
Not measuring the right metrics can lead to missed opportunities for waste reduction and efficiency improvements. Establishing effective KPIs provides clarity and direction.
- Define Relevant KPIs: Identify key metrics related to waste and efficiency in your manufacturing processes to accurately measure performance.
- Monitor and Report Regularly: Create a routine for tracking and discussing KPIs with your team to maintain focus on waste reduction initiatives.
- Adjust Strategies Based on Data: Use KPI insights to make informed decisions and refine manufacturing processes for ongoing improvement.
5. Lean Manufacturing
Manufacturing processes plagued by excess can result in waste and reduced efficiency. Lean manufacturing principles aim to minimize waste while maximizing value.
- Adopt Lean Principles: Implement the core tenets of lean manufacturing to identify value streams and eliminate activities that do not add value.
- Use Value Stream Mapping: Visualize the entire production process to pinpoint areas of waste and develop targeted action plans for improvement.
- Engage All Employees: Involve your workforce in lean initiatives to ensure everyone contributes to and understands the importance of waste reduction.
6. Employee Engagement
When employees are disengaged, they may overlook opportunities for process improvement, leading to higher waste levels. Engaging employees is essential for driving efficiency.
- Foster a Collaborative Culture: Create an environment where team members are encouraged to share ideas for improving processes and reducing waste.
- Recognize Contributions: Acknowledge and reward employees for suggesting successful waste reduction initiatives to motivate ongoing participation.
- Conduct Regular Workshops: Organize skill-building sessions to equip staff with the knowledge needed to identify and eliminate waste effectively.
7. Material Usage Analysis
Wasting materials not only increases costs but also impacts overall product quality. Analyzing material usage helps reveal inefficiencies in production processes.
- Implement Material Tracking Systems: Use software to monitor material usage and identify patterns that lead to wasteful practices.
- Conduct Material Audits: Regularly review material consumption to spot discrepancies and areas for optimization throughout the production line.
- Incorporate Supplier Feedback: Work with suppliers to gain insights on material efficiency and incorporate improvements into your manufacturing process.
8. Statistical Process Control
Variability in manufacturing processes can lead to waste and defects if not carefully monitored. Statistical Process Control (SPC) provides a framework for maintaining consistency.
- Implement Control Charts: Utilize control charts to monitor process performance and identify when variations occur, allowing for timely corrective actions.
- Train Your Team: Ensure your team is knowledgeable about SPC techniques and tools, enabling them to maintain control over manufacturing processes.
- Analyze Data Trends: Regularly review process data to identify trends and take proactive measures to mitigate variability and associated waste.
9. Data Analytics Integration
Manufacturers often overlook valuable insights hidden within their production data, which can reveal waste and inefficiencies. Integrating data analytics can transform your operations.
- Utilize Advanced Analytics Tools: Leverage data analytics software to extract insights from production data, informing waste reduction initiatives.
- Create Real-Time Dashboards: Develop dashboards that visualize key data points to enhance decision-making and response times to inefficiencies.
- Invest in Predictive Analytics: Implement predictive analytics to forecast trends and anomalies, allowing for proactive waste management strategies.